Es ist
sicherlich unbestritten, daß zu einer gelungenen
Atmosphäre einer Gartenbahn auch eine authentische
Geräuschkulisse eine nicht unwesentliche Rolle spielt.
In erster Linie sind dafür die verschiedensten
Signaltöne als auch Lauf- und Antriebsgeräusche der
Modellokomotiven verantwortlich.
Schon seit langem bietet die Industrie zu diesem Zweck
Soundmodule an. Während konventionelle Soundbausteine
die Geräusche mittels diskreter Elektronik generieren,
liegt modernen Modulen das Prinzip der Samplewiedergabe
zu Grunde. Das heißt, akustische Aufnahmen einer
Originallok liegen in digitalisierter Form im Speicher
vor und werden on demand abgespielt.
Schade nur um den besten und teuersten Soundbaustein,
wenn der wiedergegebene Sound dann nicht zur Situation
paßt. Das betrifft insbesondere die Geräusche des
Antriebes in Bezug auf die Lokgeschwindigkeit. Bei
Dampfloks sind das die Auspuffschläge, welche
unabhängig von der Geschwindigkeit immer radsynchron
vorhanden sind. Da die Zylinder i.d.R. doppelseitig
arbeiten, produziert jeder dieser Antriebszylinder 2
Auspuffschläge pro Radumdrehung. In den meisten Fällen
handelt es sich in unserer Baugröße um Modelle von
2-Zylinderlokomotiven deren Antriebszylinder mit einem
Versatz von 90 Grad auf die Treibräder wirken. Das
ergibt demzufolge 4 Dampfschläge pro Radumdrehung,
welche auch beim Modell erzeugt werden müßten.
Es stellt sich natürlich die Frage nach dem Sinn des
ganzen Aufwandes. Der nicht so anspruchsvolle
Modellbahner legt da sicherlich weniger Wert darauf und
ist zufrieden, wenn die Häufigkeit des Dampfgeräusches
irgendwie einer geschwindigkeitsbezogenen
Änderung unterliegt, Profis erwarten mehr.
In der Regel laufen diese Lösungen bisher auf eine
radsynchrone Variante mit 2 Dampfschlägen/Radumdrehung
hinaus. Da der durchschnittliche Gartenbahner meistens
immer eine höhere als vorbildgerechte
Modellgeschwindigkeit fährt, ist das sicherlich ein
annehmbarer Kompromiß, der auch so von der Industrie in
den besseren Modellausstattungen angeboten wird. Jedoch
bei Langsam- oder Rangierfahrt ist dieser
Betrug ersichtlich.
Richtig wären natürlich 4 Dampfschläge/Radumdrehung,
was den durchaus positiven Nebeneffekt mit sich bringt,
daß der Modellbahner allein der Akustik wegen sich an
die vorbildgerechte Modellgeschwindigkeit hält. Auch die
immer zu kleine Gartenbahnanlage wirkt dadurch subjektiv
größer.
Ein Dampfschlag pro Radumdrehung ist von vornherein zu
verneinen und erinnert eher an einen uralten Traktor als
an eine Dampflok.
Viele Soundmodule besitzen zur Synchronisierung des
Dampfgeräusches einen Eingang, um einen externen
Impulsgeber wie z.B. Reedkontakt oder Hallsensor
anzuschließen. So simple diese Technologie in der
Theorie funktioniert, in der praktischen Umsetzung sind
jedoch einige Besonderheiten zu beachten, wenn man ein
rhythmisches Dampflokgeräusch erreichen möchte. Fehler
im Abstand und Winkel der einzelnen Magnete lassen den
Dampfsound unschön humpeln. Hier ist eine
hohe Genauigkeit nötig!
Bei der Auswahl der Magnete sollte auf eine kleine
Bauformen zurückgegriffen werden. Je kleiner um so
besser, jedoch müssen sie noch kräftig genug sein, daß
sie den Reedkontakt noch in etwas Abstand zuverlässig
schließen. In meinem Fall wurden Miniaturmagnete in den
Dimensionen 4x4x3 mm verwendet. Erfahrungsgemäß können
herstellungsbedingte Toleranzen in Stärke und Verlauf
des Magnetfeldes vernachlässigt werden, sofern man diese
aus einer Charge kauft. Beim späteren Einbau ist jedoch
darauf zu achten, daß diese keine Beschädigung
aufweisen. Geringe Formänderungen - z.B. durch
abgeplatzte Splitter oder auch Haarrisse - können
verheerende Folgen haben!
Die größte Hürde ist die genaue Plazierung und
Befestigung der Magnete. Versuche, diese per Hand im
Außenbereich des Getriebekastens zu befestigen, sind zum
Scheitern verurteilt. Es ist wahrscheinlich unmöglich,
diese exakt mit 90 Grad Winkelabstand an den Rädern
anzubringen. Hinzu kommt, daß sie dort evtl. optisch von
Nachteil sind. Auch die Gefahr des Verlustes durch
mechanische und klimatische Beanspruchung sollte nicht
unterschätzt werden. Aber meistens sind sie einfach
schlicht nur im Weg und man findet dort sowieso keinen
geeigneten Platz.
Fast zwangsläufig ergibt sich nur der Ausweg einer
Montage, gebunden an eine Radachse im Inneren des
Getriebes. Sinnvoll ist es, die Magnete auf einem
möglichst großem Umfang zu verteilen, um die hörbaren
Folgen von Ungenauigkeiten in der Platzierung zu
minimieren. Diese sind fertigungsbedingt nie vollständig
auszuschließen.
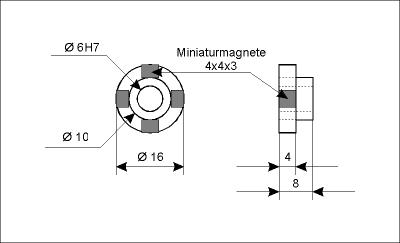 |
Skizze /
Entwurf |
Im folgenden wird
eine Lösung zur Fertigung eines Magnetträgers
vorgestellt, der als Funktionsmuster in der heimischen
Werkstatt entstand. Alle Maßangaben beziehen sich auf
diesen Prototyp, welches für eine LGB 21701 (U-Reihe)
entwickelt wurde und in vielen anderen Modellen auch
eingesetzt werden könnte. Änderungen in den
Platzverhältnissen, die zu Abweichungen in den
Maßangaben führen, sind beim Nachbau individuell
abzustimmen.
Als Material kommen nicht magnetischen Metalle in Frage,
feste Kunststoffe sind ebenso denkbar, die Auswahl
entscheidet sich in der Restekiste des Modellbauers. Im
vorliegenden Fall wurde Aluminium verwendet.
Zuerst kommt die Drehmaschine zum Einsatz. Nach dem
Plandrehen einer Stirnseite wird die Achsbohrung
angebracht. Wer die Möglichkeit hat die Bohrung auf das
Maß 6H7 zu reiben, sollte davon Gebrauch machen und
spart sich damit ein späteres Festkleben des Bauteils.
Danach wird der Außendurchmesser auf den maximal
möglichen Außendurchmesser abgedreht. Dieser richtet
sich nach den räumlichen Begrenzungen im Getriebekasten
und nach der Dicke des Reedkontaktes, der auch noch
dazwischen Platz finden muß. Werden diese Dreh- und
Bohrarbeiten durchgeführt ohne dabei das Werkstück
umzuspannen, wird auch auf einer schlechteren Drehbank
eine ausreichend hohe Rundlaufgenauigkeit erreicht.
Anschließend werden die Nuten zur Aufnahme der Magnete
ausgefräst. Ein Rundtisch oder Teilapparat ist erheblich
von Vorteil und ermöglicht die notwendige Präzision. Es
kommt dabei weniger auf eine absolut 100%ige Mittig- und
Winkligkeit der Nuten an, als vielmehr auf den
einwandfreien Rundlauf des eingespannten Drehteils (ggf.
Meßuhr verwenden) und dem exakten Drehwinkel von 90
Grad.
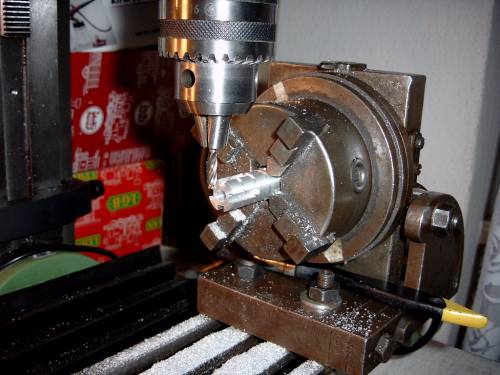 |
Fräsen
der Nuten |
Entsprechend der
notwendigen Nutenbreite wird ein passender Fräser
ausgewählt, die Magnete müssen sich später leicht
einsetzen lassen ohne jedoch zu klappern. Ein
strammer Sitz birgt die Gefahr der Beschädigung der
Magnete bei deren Montage. Die Tiefe richtet sich nach
der Dicke der Magnete.
Nach dem Absägen und sorgfältigen Entgraten des
Werkstückes werden die Magnete eingesetzt und fixiert.
Dazu wird es mit der plangedrehten Stirnseite auf ein auf
ebener Unterlage liegendes Stück Klebestreifen fixiert.
Anschließend werden die Magnete eingesetzt und auf das
Klebeband gedrückt, so daß diese bündig mit der
Stirnseite abschließen und am Nutgrund anliegen.
Bei dem Einsetzten der Magnete ist auf folgende wichtige
Kleinigkeit zu achten: Die Polarisierung der Magnetfelder
wird wechselseitig ausgerichtet, d.h. Nord- und Südpole
wechseln sich am Umfang ab. Das hat wesentlichen Einfluß
auf Verlauf und Abgrenzung der Magnetfelder und damit auf
die am Reedkontakt wirkenden Kräfte.
|
Nach einer letzten
Überprüfung des korrekten Sitzes werden die Magnete mit
geeignetem dünnflüssigen Klebstoff oder Sicherungslack
befestigt.
Nun wird noch die abgesägte Seite des Werkstücks
vorsichtig auf Maß gedreht und der Bund
herausgearbeitet, so daß der nun fertig gestellte
Magnetträger bequem auf der Achse im Getriebekasten
Platz findet. Dabei ist das seitliche Spiel der Achsen
ist zu beachten und darf nicht behindert werden, welches
aus Gründen der Kurventauglichkeit durchaus einige
Millimeter betragen kann.
Natürlich sollte man sich vor Beginn der Arbeiten über
die Einbauposition von Magnetträger und Reedkontakt
weitestgehend im Klaren sein und unbedingt eine durch den
Motor angetriebene Achse auswählen. Untauglich sind
Achsen, die über die Kuppelstangen mitgenommen werden.
Durch das massive Spiel der Kurbelzapfen ist eine
gleichmäßige, ruckelfreie Rotation der Achse und damit
ein rhythmisches Dampfgeräusch aussichtslos.
Nachdem die Achse ausgebaut und das entsprechende Rad
abgezogen ist, wird der Magnetträger mittels eines
passenden Stück Rohres, Hülse o. ä. mit vorsichtigen
Hammerschlägen aufgeschoben (Vorsicht: die Magnete
dürfen dabei nicht beschädigt werden!). Nun wird das
Rad unter Beachtung des Winkels der Kurbelzapfen und der
Spurbreite aufgesetzt und die präparierte Achse kann
wieder eingebaut werden.
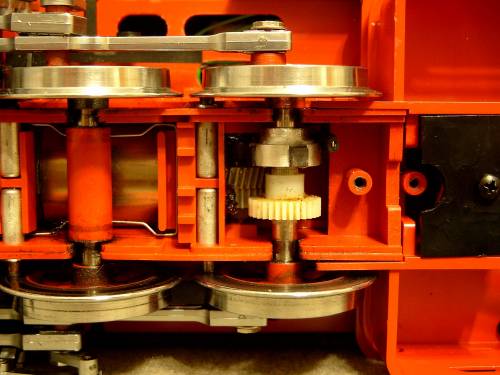 |
rechts neben
dem Magnetträger steht hochkant der Reedkontakt |
Zum Schluß wird
noch der Reedkontakt eingebaut und justiert. Dieser muß
so positioniert werden, daß dieser trotz des seitlichen
Spieles der Achse von den Magneten immer sicher auslöst.
Schon aus Gründen des Platzbedarfes sind kleine
Bauformen zu bevorzugen. Diese haben meistens darüber
hinaus den Vorteil, daß sie schnellere Schaltzyklen
zulassen und selbst bei vorbildwidrigen
Höchstgeschwindigkeiten immer noch zuverlässig
arbeiten. In meinem Fall fand ein
Glasrohr-Miniaturreedkontakt 14 x 2,2 mm Verwendung. Wenn
man diesen vorher mit einem Stück Schrumpfschlauch
überzieht läßt er sich nach erfolgreichem Test und
Probelauf (R1-Schlängelkurse und Weichenstraßen sind
besonders geeignet) mit einem Tropfen Klebstoff fixieren.
Damit ist der mechanische Teil abgeschlossen.
Zur Verdeutlichung der notwendigen Genauigkeit sei an
dieser Stelle erwähnt, daß Herstellungsfehler sich um
den Faktor Pi am Umfang vervielfachen können. Der nach
dieser Methode gefertigte Prototyp wies eine am Umlauf
gemessene Distanzabweichung der Magnete von etwa +/-0,25
mm auf, die Ungenauigkeiten im Rundlauf lagen bei ca.
+/-0,1 mm. Rechnerisch ergeben sich daraus Differenzen
von ca. +/-2 Grad (am Viertelkreis), hörbare
Rhythmusstörungen konnten jedoch nicht
festgestellt werden.
Die hier vorgestellte Methode stellt nur eine
Möglichkeit der Fertigung eines solchen Bauteils dar und
orientiert sich an den zur Verfügung gestandenen
Werkzeugen und Maschinen und ohne Anspruch auf
Optimierung des Prozesses für eine Serienfertigung. Der
interessierte Bastler findet sicher auch andere Wege der
Realisierung und sollte die hier beschriebenen
wesentlichen Grundlagen als Anregung berücksichtigen.
Modellbauer, denen eine CNC-Fräsmaschine zur Verfügung
steht, sind natürlich klar im Vorteil.
Präzisionsgeschnittene Magnetträger, Magnete und
Reedkontakte hier erhältlich.
|